For an engineer, testing is just as crucial as designing. No numerical simulation or projection can ever replace a comprehensive testing campaign. As our 6S CubeSat enters Phase D, the final stage dedicated to testing and production, it is essential to assess its structural integrity and thermal properties.
Consequently, from February 24th to 28th, the Thermal Division of the 6S CubeSat conducted a thermal test at ESTEC, the ESA facility in the Netherlands specializing in the production and testing of CubeSats. This opportunity was made possible through 6S CubeSat’s participation in ESA’s “Fly Your Satellite! Testing Opportunities” program.
Let’s explore what they accomplished, the challenges they tackled, and the milestones reached by our incredible students.
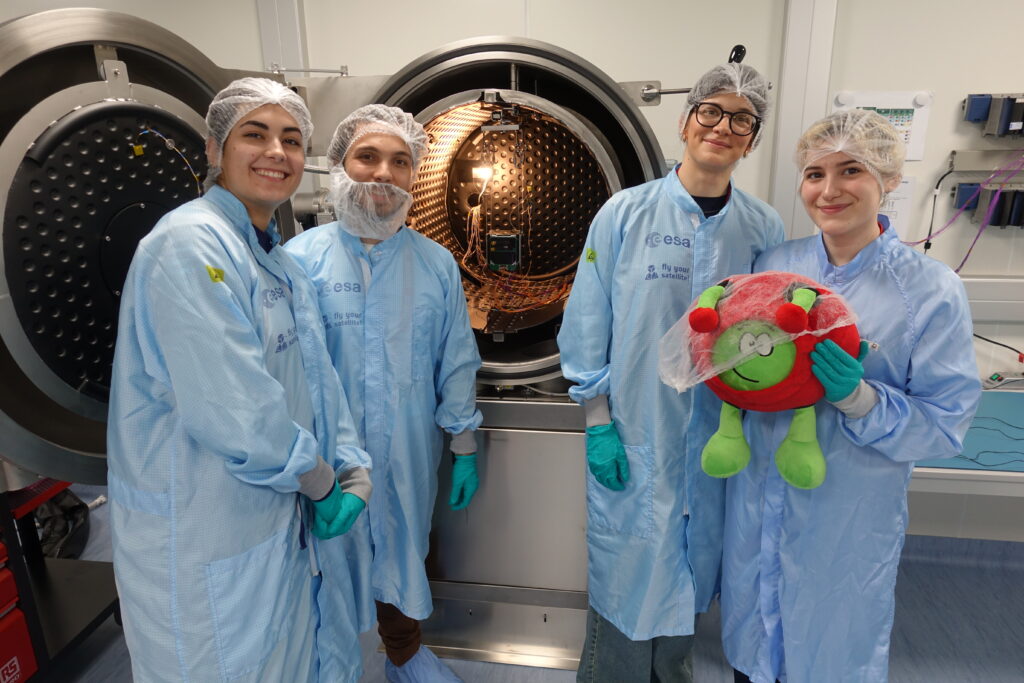
WHY PERFORM A THERMAL TEST?
In high-cost sectors like space exploration, the design phase cannot rely on constant testing campaigns. Organizing a test expedition is extremely expensive, especially for student-led projects, which often have only one opportunity for execution. However, designing a system effectively requires monitoring how changes influence its behavior.
To overcome this challenge, we use ESATAN, a finite element software service for thermal simulation, to predict the CubeSat’s thermal response under various conditions. This ESA software can calculate view factors, perform orbital simulations, and solve heat flux equations.
However, despite years of refinement, the thermal model represents only an approximation of the CubeSat’s thermal properties. The materials used in numerical models reflect averaged properties, but no software can fully account for the effects of surface treatments and processing. These processes create dislocations that alter local specific heat capacity and conductivity, making precise thermal predictions challenging.
For instance, our 6S CubeSat contains 500 nodes, which is relatively few. Even under these conditions, thermal simulations can produce errors of up to fifteen degrees. This makes it clear that testing is not just a design step but an absolute necessity in any project.
HOW TO PERFORM A THERMAL TEST?
The thermal test relies on the use of a TVaC (thermal vacuum chamber), a room where vacuum is created using pumps, and temperature is controlled externally. By creating the vacuum, we simulate the absence of convective heat transfer which happens in space. Moreover, we are able to control the radiative heat transfer by controlling the temperature of the TVAC walls. Temperature sensors are placed at strategic points inside the chamber; particularly at locations most likely to be affected by potential numerical errors. The structure is then subjected to several thermal cycles, while simultaneously, a mathematical model is developed to simulate the real-world conditions. Anyway it will take more than a month to correctly develop this part and we will discover the results further.
However, due to the potential for structural damage, which would be critical for the actual satellite, the team used a Thermal Structural Model (STM). This model replicates the thermal and structural properties of the real design but is constructed from more affordable materials. It excludes electronic components, batteries, and computers, which are only simulated. For the 6S CubeSat, the Structural Thermal Model (STM) was developed with the support of CTI Aerospace, one of our sponsors.
Model correlation involves comparing simulated results with real data collected during testing. This step is crucial in assessing the accuracy of our thermal design. It is particularly significant for thermal parameters with higher uncertainty, both in thermo-optical and thermophysical aspects. In this test, the team subjected the STM to temperatures ranging from 0 to 45 degrees, covering both the lowest and highest expected limits.
Model correlation consists of calibrating the model by adjusting, refining, and comparing numerical results with experimental data. This process reduces discrepancies between simulated and real data, ultimately yielding a model that provides reliable and accurate results.
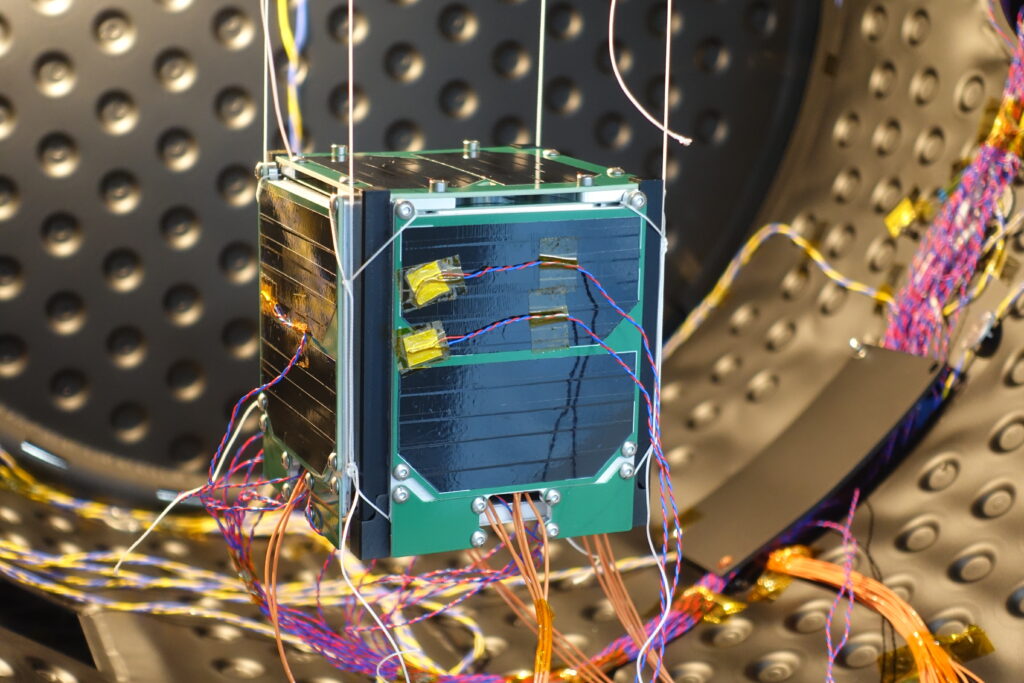
HOW DID WE HANDLE THE TESTS?
By speaking with Ludovico Bernasconi, the TCS (Thermal Control Subsystem) team leader, we can gain insight into how the tests were conducted at ESA’s facilities.
“First, we prepared the satellite with the final adjustments. For example, we soldered the last electrical circuits and completed the thorough cleaning of the satellite. Once that was done, we set up the TVAC by placing the thermistors—resistive sensors that measure temperature through changes in material resistance—and the heater inside the satellite to control temperature variations from the external environment.”
After completing the final adjustments, the TVAC was sealed with our CubeSat inside. The team then waited for three days to observe the results. During this time, the CubeSat underwent several thermal cycles, alternating between hot and cold points of average temperature. Although the most extreme conditions might seem the most important to analyze, the team opted to test a range of balanced conditions to capture a variety of structural and thermal behaviors. Indeed, in the process of model correlation is much more useful to have several tests to obtain the best possible model.
The test lasts a long time due to the need to reach thermal equilibrium, known as a plateau. Achieving perfect thermal balance is impossible, as thermal phenomena are always present; instead, equilibrium is approached asymptotically. To determine when the plateau is reached, we assess the time required for the temperature to change by one degree. Once this time falls below a predetermined threshold, the system is considered to have reached the plateau.
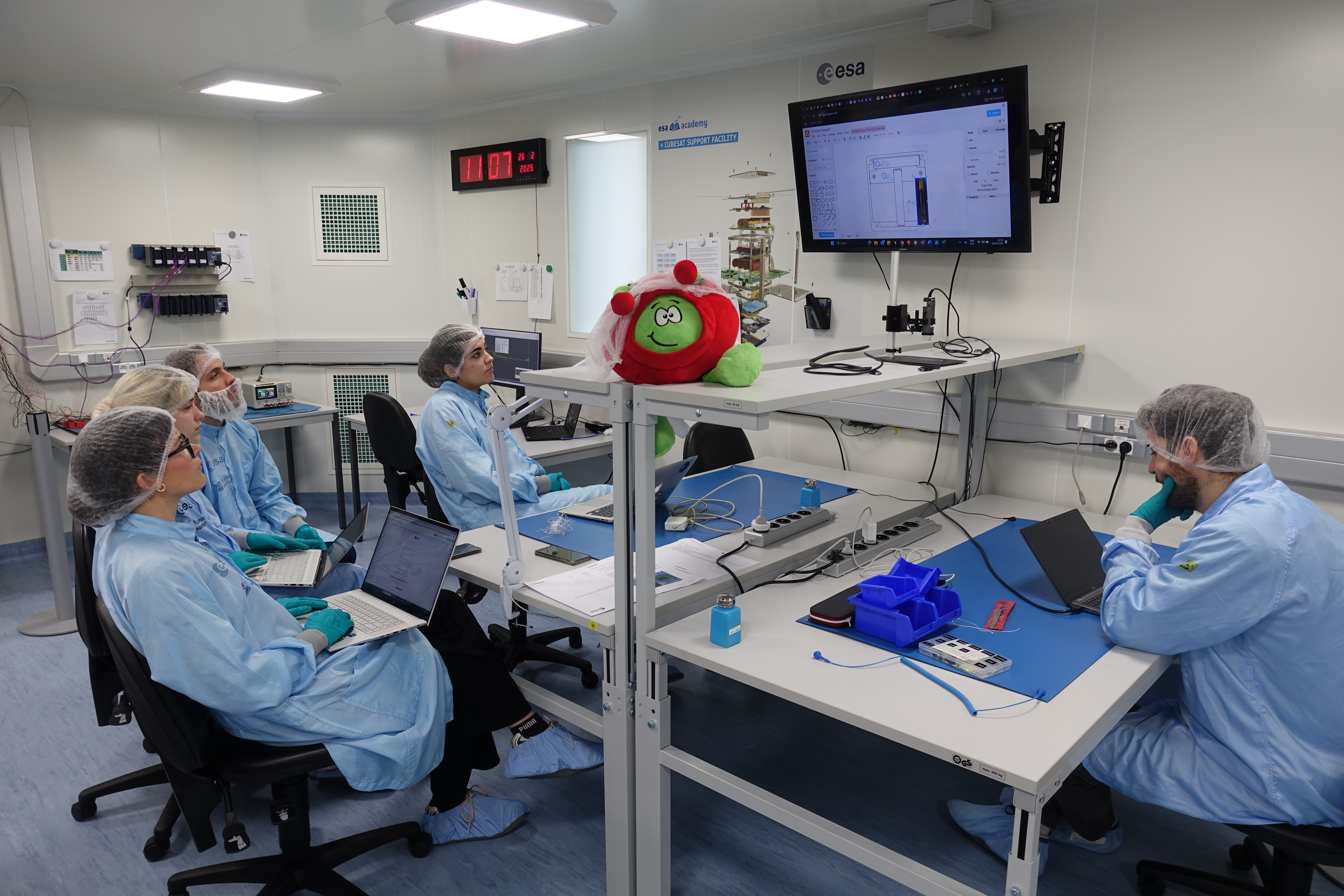
HOW DID IT GO?
To conclude, in the words of ESA’s engineers, the practical test has been a success. Now, we must assess the differences between the data and the model. In any case, we can confidently say that PoliSpace’s main project, the 6S CubeSat, is becoming increasingly tangible. As we enter Phase D, we can look back with pride and satisfaction, knowing that we are achieving key milestones day by day.